
With high temporal and spatial resolutions, synchrotron radiation-based ultrafast X-ray techniques enable the monitoring of microstructural dynamics during the AM process in situ and in real time 17, 18. The direct characterisation of dynamic behaviours in the melt pool is very challenging and remains unknown, hindering a deep understanding of the rapid melting and solidification behaviour of SX superalloys. However, previous studies are mainly based on the characterisation of the recovery specimens and numerical simulations. Very recently, SX nickel was manufactured by a flat-top laser 16. controlled the selective electron beam melting process window and successfully fabricated SX superalloys on stainless steel substrates after growth competition of different grains in the first few layers without a separator and seed crystals. investigated 13 the influence of the processing parameters on the deposited productivity and epitaxial SX growth in the LMD process by the orthogonal experiment method. developed 12 a self-consistent 3D mathematical model to predict the crystal growth and microstructure formation in the LMD of SX superalloys. demonstrated 11 that the deposition of René N4 nickel superalloy grows epitaxially and inherits the orientation of the substrate, presenting a columnar dendritic structure with orientation during laser melting deposition (LMD). There have been numerous investigations on the epitaxial growth of nickel-based SX superalloys during AM processes.
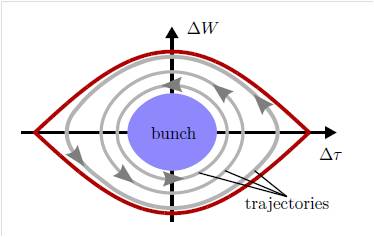
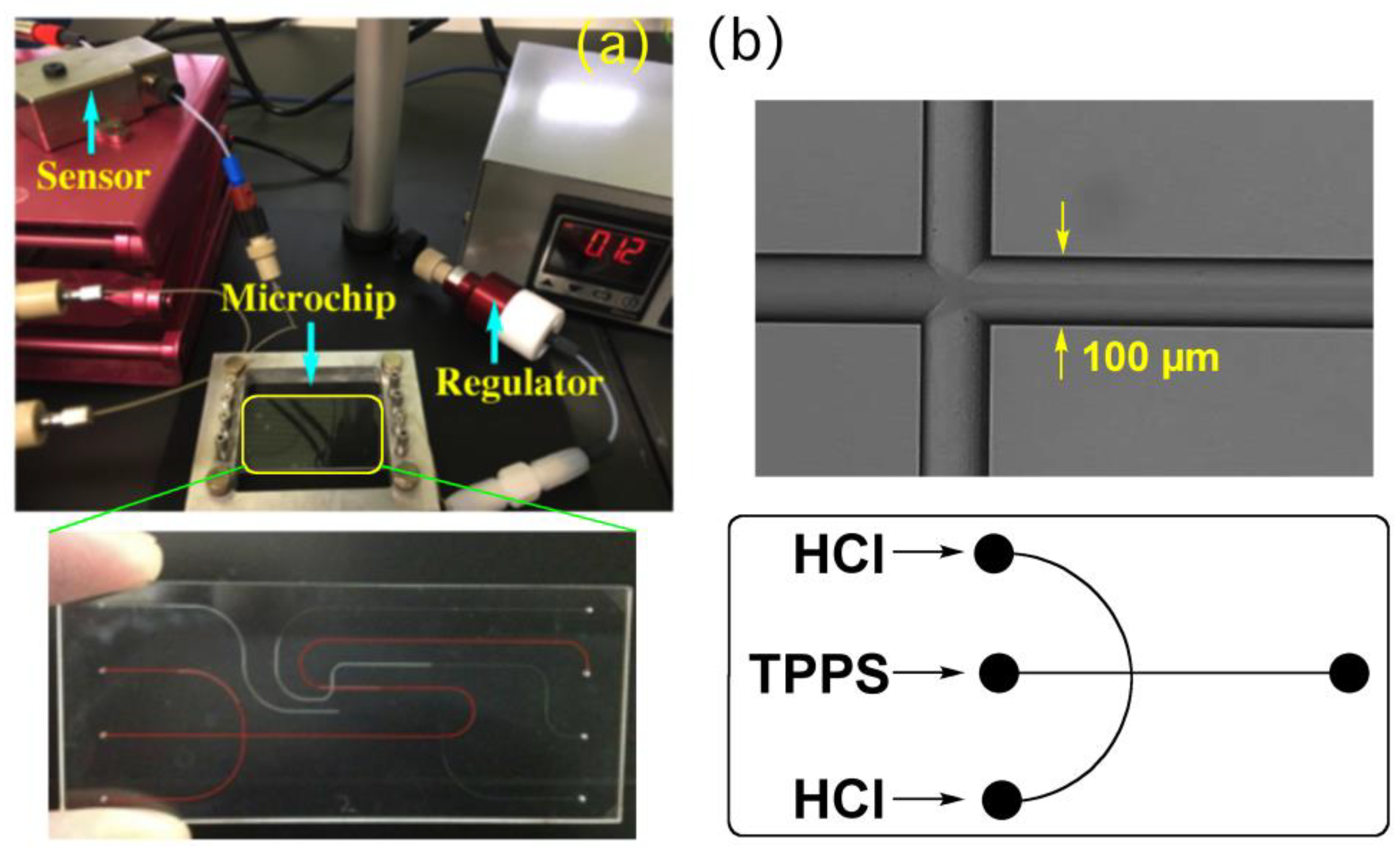

However, for nickel-based single-crystal (SX) superalloys used in high-temperature environments, using the epitaxial growth characteristics of AM to obtain directional or single-phase alloys is essential. As a consequence, the prominent microstructural feature of printed metallic materials is columnar grains that grow epitaxially from the melt pool boundary 5, 6, 7, 8, which is often undesirable for industrial applications 9, 10. During the manufacturing process, the metal powder is melted instantly, and a microscale molten pool forms in a short time under the operation of a high-energy laser or electron beam, achieving steep temperature gradients of up to ~10 7 K m −1 and ultrahigh cooling rates of ~10 7 K s −1 4. Additive manufacturing (AM), such as selective laser melting (SLM) and direct energy deposition (DED), is driven by a three–dimensional (3D) digital model and used in the direct manufacturing of complex structures without any moulds moreover, this process has been considered a revolutionary breakthrough in the field of manufacturing technology 1, 2, 3.
